Pumps are the heart of hydraulic systems, which literally “pump” fluid to deliver the energy needed to power movement. This is an important action, and one that promotes a variety of questions.
Let’s begin by summarizing how hydraulic pumps operate.
Hydraulic pumps are responsible for converting mechanical energy into hydraulic energy. The resulting mechanical energy powers the motors in a hydraulic system.
Pumps provide this mechanical action by performing two functions:
End-users and distributors alike may have questions about how they function, when they don’t, or how to problem solve solutions to common issues.
Let’s walk through some frequently asked questions about hydraulic pumps and end by assuring you that when it comes to our line of hydraulic pumps, we supply top-notch service and quality at HPS.

A: There are several potential outcomes depending on the pump and design. Here are the most common:
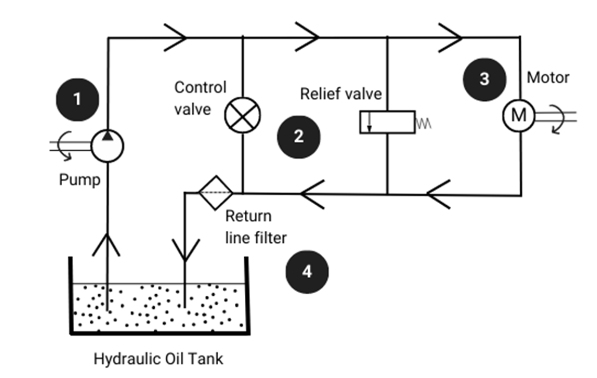
Keeping fluid clean assures the user of a cost-effective approach to vane pump maintenance that allows the price of the filters to be quickly recovered by savings from improved performance and oil life.
For more on protecting vane pumps from contamination, visit Eaton’s Guide to Systemic Contamination Control.
At HPS, every person we choose to involve in the process — from our suppliers to remanufacturers to distributors to the end users — has a passion for delivering quality and a desire to work with the best.
To do so, HPS maintains four unique standards that we absolutely will not waver on:
Hydraulic Parts Source is a leading fluid power remanufacturer, and we’re ready to serve you. Contact us today to experience OE quality for a fraction of the time and cost by calling (866) 985-8401 or get a quote by emailing sales@hydparts.com.
Let’s begin by summarizing how hydraulic pumps operate.
Hydraulic pumps are responsible for converting mechanical energy into hydraulic energy. The resulting mechanical energy powers the motors in a hydraulic system.
Pumps provide this mechanical action by performing two functions:
- Creating a vacuum at the pump inlet that allows pressure to force liquid from the reservoir into the inlet line
- Delivering fluid to the pump outlet and into the hydraulic system
End-users and distributors alike may have questions about how they function, when they don’t, or how to problem solve solutions to common issues.
Let’s walk through some frequently asked questions about hydraulic pumps and end by assuring you that when it comes to our line of hydraulic pumps, we supply top-notch service and quality at HPS.
Frequently Asked Questions About Hydraulic Pumps
Q: Which Type of Pump Should I Use?
A: Many hydraulic pump brands offer pumps that meet various specifications based on common features and types. In general, there are three major types of pumps in a hydraulic system:

- Gear pumps are economical, reliable, durable, and easy to install. However, they become inefficient over time and tend to be noisy when operating.
- Vane pumps are more efficient than gear pumps but less efficient than piston pumps. Advantages include many control options (such as pressure compensation, load sensing, and displacement controls) and less noisy. There are a few areas where a vane pump is not a suitable solution, such as when an application requires a high-viscosity fluid at high pressure.
Image: Power & Motion - Piston pumps can handle high pressure, are efficient (95%), and have nearly infinite methods of control. The downsides are that they are more expensive to purchase and repair and require complex service, which is unfortunate considering the mechanical parts in a piston pump are also more prone to wear.
Q: What Happens When Pump Rotation is Reversed?
A: There are several potential outcomes depending on the pump and design. Here are the most common:
- Reduced flow
- Noise
- Seal failure
- Bearing failure
- Loose impeller, which can damage the pump
Q: Where Is the Pump Located Within a Hydraulic System?
A: Pumps are located between the fuel reservoir and motor, and both are easy to spot on a schematic.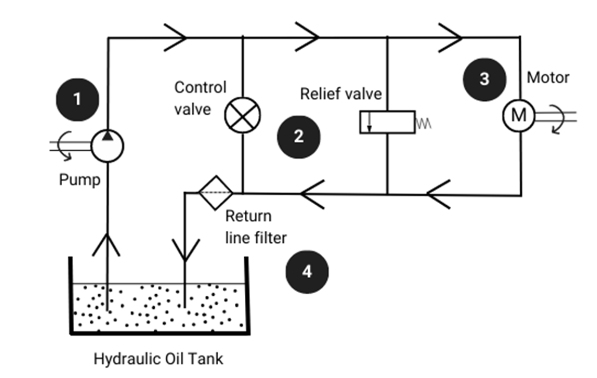
The pump-motor connection is important to note, as motors are the prime movers used to rotate hydraulic pumps.
Motors are easy to spot, represented by the letter “M” inside a circle (3). A curved arrow (like in the illustration) represents the direction of shaft rotation.
Hydraulic pumps (1) do not look much different than motors on the schematic, as they are represented by a circle with a black triangle that points to which direction flow will go in. If the triangle is clear, it indicates a pneumatic pump (or compressor).
Q: Why did my Vane Pump Stop Flowing?
A: Vane pump failures most often happen after an overload, a leak, or a specific event that is visibly evident or that some easy trouble-shooting can uncover. However, more than 80% of all failures in vane-type pumps can be traced back to a single cause: dirty hydraulic fluid.Keeping fluid clean assures the user of a cost-effective approach to vane pump maintenance that allows the price of the filters to be quickly recovered by savings from improved performance and oil life.
For more on protecting vane pumps from contamination, visit Eaton’s Guide to Systemic Contamination Control.
Q: What is the Pressure on a Vickers Vane Pump?
A: Vickers VMQ pumps provide continuous pressure ratings up to 293 bar (4,250 psi) for the 25-frame size and displacements up to 488 cm3/r (29.78 in 3/r) with the triple pump version.?HPS Values Quality Pumps
As already mentioned, pumps are pivotal instruments in producing hydraulic power. We strive to supply quality pumps and services to keep hydraulic motors running.At HPS, every person we choose to involve in the process — from our suppliers to remanufacturers to distributors to the end users — has a passion for delivering quality and a desire to work with the best.
To do so, HPS maintains four unique standards that we absolutely will not waver on:
- Great Customer Service
- Best Quality Products
- Value Added Suppliers
- Immediate Availability
Hydraulic Parts Source is a leading fluid power remanufacturer, and we’re ready to serve you. Contact us today to experience OE quality for a fraction of the time and cost by calling (866) 985-8401 or get a quote by emailing sales@hydparts.com.
Tags
hydraulic
pump
valve
pumps
troubleshooting
vickers
faq
valves
motors
hydraulics
rexroth
denison
repairs
downloads
motor
hydraulic test stand
hydraulic industry
market
system
pascal
hydraulic fluid
overflow
overfill
excavator
dension
vane pump
corrosion
pump sound
valve sound
prv
cold
fluid
schematic
remanufacturing
Posts
2024
August
2023
Need a Quality Supplier? HPS Checks All the Marks
[08/29/24 04:12 PM]
Digitization & Hydraulics
[08/29/24 03:45 PM]
May
Hydraulic System Troubleshooting: Step-By-Step
[05/23/24 01:38 PM]
Downloadable Resources for Distributors
[05/01/24 11:28 AM]
April
February
Meet Our New Hydraulic Test Stand: Part 2
[02/15/24 02:50 PM]
Remanufacturing Benefits for End-Users
[02/01/24 03:04 PM]
January
December
2022
Hydraulic Systems and Their Components: An Overview
[12/20/23 12:27 PM]
Overfilling Hydraulic Fluid Can Cause Issues, Too
[12/08/23 01:18 PM]
November
Branded Gifts for Commuting Hydraulics Clients
[11/09/23 08:41 PM]
Diagnosing Pump Problems on Construction Equipment
[11/08/23 01:42 PM]
October
The Useful Complexity of Proportional Control Valves
[10/25/23 09:11 PM]
FAQs: Let’s Talk About Hydraulic Pumps
[10/23/23 08:25 AM]
Hydraulics System Corrosion FAQs
[10/11/23 01:00 PM]
September
August
5 Ways Inside Reps Can Boost Hydraulics Sales
[08/13/23 03:54 PM]
Positive Displacement Pump FAQs: How Do Hydraulic Vane and Gear Pumps Work?
[08/10/23 06:15 PM]
The Value of Hydraulic Pressure Relief Valves
[08/02/23 05:26 PM]
July
June
May
Hydraulic Parts Source is So Much More Than Pumps, Valves, and Motors
[05/30/23 12:09 PM]
How Does a Hydrostatic Pump Work?
[05/15/23 11:07 AM]
April
How Do Directional Control Valves Work?
[04/27/23 10:37 AM]
From Valves to Motion: Knowing How a Cylinder Works to Move a Hydraulic System
[04/14/23 10:23 AM]
March
HPS Troubleshooting Tactics: Common Hydraulic Valve Issues
[03/15/23 10:47 AM]
What Happens When Hydraulic Parts Suppliers & Distributors Join Forces?
[03/15/23 10:04 AM]
February
January
December
November
October
September
August
July
June
2021
Denison’s Innovative Beginnings Show Through in Quality, Flexible Parts
[06/20/22 06:38 PM]
Our Products: Get to Know True Blue Vickers
[06/06/22 06:30 PM]
May
Pascal’s Principle and the Origin of Hydraulics
[05/31/22 06:25 PM]
Avoiding Devastating Cavitation Damage
[05/03/22 06:16 PM]
April
Hydraulic Parts: How to Make Green Choices
[04/18/22 06:09 PM]
Hydraulic System Hazards: Avoiding Safety Issues from the Beginning
[04/05/22 05:58 PM]
March
Motors 101: Hydraulics at Work
[03/21/22 07:00 PM]
Valves 101: It’s All About Control - and Some Other Need-to-Know Facts
[03/07/22 06:53 PM]
February
January
December
November
2020
Promotional Gift Ideas for Fluid Power Distributors to Unwrap Marketing Potential
[11/29/21 10:00 AM]
Need-to-Know Fluid Power Facts: The 5 W's of Hydraulic Oil Viscosity
[11/29/21 09:32 AM]
How to Close the Sales Gap & Increase Revenue: Part 2
[11/08/21 08:06 PM]
October
September
August
July
June
Change Filter Elements to Avoid a Hydraulic System Nightmare
[06/07/21 05:02 PM]
5 Sources of Hydraulic Fluid Contamination (and How to Address Them)
[06/01/21 04:09 PM]
April
How to Win Back Lost Customers: 5 Steps for Fluid Power Distributors
[04/19/21 04:03 PM]
7 Outside Sales Strategies to Drive Fluid Power Revenue
[04/05/21 03:54 PM]
March
4 Reasons Fluid Power Distributors Should Consider Promotional Gifts
[03/16/21 03:48 PM]
Hydraulic System Corrosion: 3 Causes & 6 Prevention Tips
[03/10/21 03:42 PM]
February
Setting and Troubleshooting Relief Valves in Hydraulic Systems
[02/23/21 03:36 PM]
When & How to Replace a Hydraulic Pump Hose Assembly
[02/08/21 03:26 PM]
January
December
3 Directional Control Valve Problems & Fixes
[12/15/20 12:22 PM]
3 Ways to Align a Hydraulic Pump
[12/01/20 12:15 PM]
November
Why Are My Hydraulic Seals Failing? 6 Common Causes
[11/16/20 12:09 PM]
8 End-User Tips for Choosing a Hydraulic Fluid Power Products Distributor
[11/02/20 12:05 PM]
October
September
8 Checks for Restarting Hydraulic Pumps After Long Shutoff
[09/29/20 11:45 AM]
6 Key Hydraulic Product Distributor Strengths
[09/21/20 11:38 AM]
8 Things to Check When Your Hydraulic Pump Stops Flowing
[09/01/20 09:47 AM]
August
3 Common Causes of Noisy Pumps and What to Check
[08/17/20 09:34 AM]
Old Cores: The Key to New Revenue for Fluid Power Distributors
[08/03/20 09:01 AM]
May